Double Hex
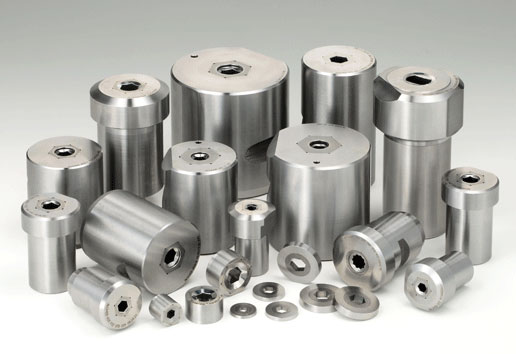
Double Hex Tooling
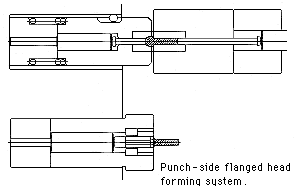
One of the problems of cold forming flanged hex-head bolts is the extreme stress at the hex corners which causes accelerated punch wear while leading to premature breakage.The unfortunate results are increased costs for the fastener maker in terms of tooling replacement,unnecessary downtime,and defective workpieces.Mitsutoyo developed the Double Hex series of tooling specifically to slove these problems.
Mitsutoyo’s Double Hex design uses wedge-shaped nib pieces assembled within a reinforcing ring and inserted into the punch case.Conventional punch tooling uses a one-piece solid nib for the forming orifice,a design which concentrates stress at the hex corners and which leads to the problems mentioned previously.The Double Hex design,however,disperses the corner stresses by allowing the impact shocks to be absorbed through the gaps between the nib segments.These stress-absorbing gaps provide the further advantage of allowing air and coolant to escape,and thus eliminate air-cushion and hydro-cushion effects.
The identical wedge shapes of the segment nibs allow for more efficient mass production to a higher level of dimensional precision.Unlike coventional one-piece punches which must be machined and hand lapped before assembly,the Double Hex punch needs absolutely no hand finishing of the forming surfaces.
The extended service life offered by Double Hex tooling increases productivity by allowing fastener makers to run the header longer,an advantage which can also be effectively utilized by unmanned production systems.Another benefit is that workpiece quality is more uniform and can be maintained throughout a longer punch service life.Double Hex tooling helping fastener makers to lower costs across the board while increasing overall productivity.These advantages are also being realized by the Double Hex tooling used for nut forming.